Por: Frederico Avillez e José Pedro Salema, Agrogestão
A CAC II - Companhia Avícola do Centro, SA é empresa que se dedica à classificação e comercialização de ovos. Localizada no concelho de Leiria, é actualmente uma das maiores empresas do género e agrupa produtores de aproximadamente um milhão de galinhas.
Actualmente, a empresa tem cerca de 80 colaboradores e o centro de classificação está dotado de equipamento e pessoal que asseguram a classificação e embalagem de cerca de 108.000 ovos por hora.
Há cerca de 5 anos a CAC II iniciou a instalação de um sistema de controlo de gestão que veio potenciar a adopção de novas práticas e aumentar drasticamente a velocidade de consulta e precisão do sistema de rastreabilidade. A motivação para a instalação de tal sistema estava ancorada não só nas exigências da grande distribuição e dos clientes estrangeiros, mas também nas necessidades de reforço do controlo de gestão.
Recepção
O controlo do processo de recepção dos ovos foi um dos objectivos centrais da implementação do sistema. Foi desenvolvido um sistema que permite a compilação de toda a informação caracterizadora do lote recebido, disponibilizando essa informação para todas as áreas da empresa. Num ecrã táctil integrado com a balança o operador processa cada lote e associa-lhe uma etiqueta com código de barras e informação para leitura humana.
O sistema está fortemente integrado com o ERP - ETICADATA, já implementado há muito na empresa. Na recepção, o sistema faz a emissão da Guia de Recepção no ERP e é o ponto de partida do processo documental de compra. O processo foi muito simplificado e veio libertar os recursos administrativos para outras tarefas.
Para José Luís Gomes, Director de qualidade, o processo de recepção de ovos está agora muito controlado. “Um bom exemplo nesta fase é a etiqueta que é colocada à chegada em todos os lotes de ovos que condensa toda a informação relevante e que anteriormente estava dispersa em diferentes suportes” afirma aquele responsável na empresa.
Classificação
Na classificação, o controlo do processo foi potenciado pela utilização de leitores de códigos de barras na entrada dos lotes para classificação. Junto das saídas de cada linha da calibradora MOBA estão disponíveis impressoras de etiquetas que, utilizando toda a informação do sistema, imprimem as etiquetas de caixa do produto, respondendo às exigências legais e logísticas dos clientes.
O funcionário responsável pela gestão da linha utiliza o leitor de código de barras para definir qual o lote que está a laborar no momento, e em ecrã próprio especifica qual a referência que está a ser “produzida” em cada uma das linhas de saída.
Os operadores que estão junto da saída accionam um botão próprio para pedir a impressão da etiqueta EAN128 que colam desde logo na caixa do produto final, ou são colocadas junto das paletes dos ovos que terão outro destino.
As caixas de produto final são desde logo colocadas num tapete rolante, que as encaminha para o equipamento que faz o seu fecho. Em paralelo com esse equipamento, foi instalado um leitor fixo de código de barras, que ao fazer a leitura da etiqueta acciona no sistema central a informação da existência de uma nova unidade de stock disponível para paletizar.
Em paralelo são registadas os custos de produção destes novos lotes produzidos, e são afectados os stocks das matérias-primas e materiais de embalamento. Toda esta informação é integrada no ERP para que fique disponível para todos os departamentos.
A paletização é realizada com recurso a um robot que só pode ser implementado pelo facto deste sistema já estar desenvolvido. O leitor fixo, referido atrás, permite ao sistema saber qual o artigo em questão, e dessa forma encaminhar para a linha de paletização automática as caixas em questão. “A instalação do robot de paletização permitiu eliminar duas pessoas dessa tarefa e libertá-las para outras funções. Tínhamos quatro pessoas nessa área e agora temos duas.”
Expedição
O processo de expedição de produto final implementado foi completamente integrado com os processos documentais da empresa. Assim, é a partir das notas de encomenda inseridas no sistema via EDI (ou facturação electrónica) que os funcionários preparam cada um dos carros de transporte. O utilizador tem disponível um ecrã onde pode consultar as notas de encomenda, e utilizando um leitor de códigos de barra sem fios, vai fazendo a satisfação da encomenda, através do “picking” directo das etiquetas de palete, ou desmanchando paletes para utilizar apenas algumas das unidades logísticas (caixas) suas integrantes.
Foi sentida uma grande mais-valia na expedição. Um indicador de qualidade muito concreto desta melhoria é a diminuição das encomendas não satisfeitas (ou satisfeitas de forma incompleta): “Reduzimos 10 vezes a nossa taxa de encomendas não satisfeitas passando de valores na ordem dos 2,4% em 2006 para os 0,26% e no último ano.”
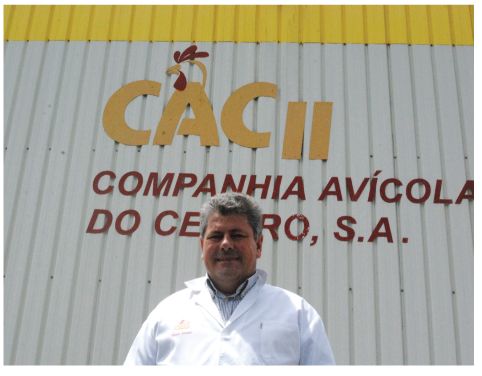
Conclusões e principais melhorias
Uma das preocupações da empresa foi a obtenção de maiores níveis de controlo em termos dos custos de produção. O sistema foi desenhado de raiz para incluir estas funcionalidades. Por outro lado não foi desenhado um sistema independente da produção para responder apenas às exigências do departamento de qualidade.
Um dos processos que beneficiou com a implementação do sistema de controlo descrito foi a auto-venda. Neste momento os vários carros que fazem a distribuição dos produtos pelas redes mais tradicionais de distribuição, fazem os documentos de venda no momento da entrega dos produtos com o respectivo. Este processo é conseguido com equipamentos de facturação portáteis com a leitura dos códigos de barra de cada caixa.
Os tempos de carga dos veículos na expedição foram substancialmente reduzidos, em paralelo com as reduções dos erros e falhas que originavam situações de incumprimento de satisfação de encomendas. E isto significa não só, uma redução de custos, mas também uma forma de não desperdiçar possibilidades de facturação.
O sistema de rastreabilidade implementado possibilita fazer o percurso de rastreabilidade ascendente e descendente. Uma das vantagens apontadas é a precisão conseguida com este sistema, que permite chegar a lotes de retirada muito mais confinados que os sistemas que habitualmente estão instalados nas empresas congéneres.
“O nosso objectivo agora é colocar o mesmo sistema a funcionar em cada um dos nossos novos centros de classificação, e desenvolver a integração de todos os sistemas.” Avança o Director Geral Manuel Sobreiro que assim assume da melhor forma a satisfação com o sistema implementado. “Temos experiência comprovada que a implementação de boas práticas de gestão traduz-se num impacto positivo nos resultados económicos e a introdução deste sistema é mais um exemplo disto” rematou aquele responsável.